THERMOFORMING
PRODUCTS
At Progressive Plastics we manufacture a range of pre-formed rigid and flexible plastic trays for New Zealand meat, fish and produce companies. Our trays help to protect and preserve quality products in premium export and New Zealand retail ready markets.

PET TRAYS
Meat and produce can be packed in these trays with an overwrap or flow pack or alternatively most of our trays are used for export meat in conjunction with a vacuum barrier bag.

LDPE BONEGUARDS
For use where additional protection is required against bone piercing other packaging. These can be flat strips, caps or fully formed trays to suit a particular cut of meat.

BARRIER TRAYS
For use in VSP and MAP applications for fresh meat, poultry and fish where premium shelf life and presentation is required. Our barrier trays have been manufactured from recycled and renewable resources and are fully recyclable.

MATERIALS
Our non-barrier trays are made from Polyethylene Terephthalate (PET) and Low-Density Polyethylene (LDPE) plastics that are manufactured from plastic sheet sourced from our supply partners in New Zealand and overseas. The use of independent external film suppliers allows us to ensure our products are made from the best quality materials and with technical structures most suited to the application.

STORAGE & DELIVERY
We hold stock of most of our product range in our warehouse. Dispatch from us is on the same day as order and we can normally deliver to most locations in New Zealand within 3 to 4 days.

ENVIRONMENTAL BARRIER SOLUTION
Our VSP and MAP trays are produced in partnership with Plantic Technologies using PLANTIC™ R sheet. This allows us to offer trays that are made from a combination of recycled PET together with a renewably sourced plant based core of PLANTIC™ HP. This core has exceptional gas barrier properties resulting in long shelf life for food products. These trays are fully recyclable in the usual PET waste streams.
Waste plastic generated from our manufacturing process is ground in to a fine flake and sent back to Plantic Technologies for re-use in their production process meaning we have a true closed loop recycling process.
Further information about the Plantic story can be found here.

PRODUCT DEVELOPMENT & TOOLING
Our engineering team has the capability to work though specific customer requirements and develop prototype trays followed by final production runs using generic and custom-made tooling.
Customers do not need to accept what is “off the shelf” for plastic trays. We can make a tray specifically to suit your requirements.
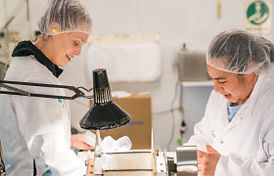
FOOD SAFETY
Our manufacturing and warehouse facility maintains HACCP Food Safety program audited annually.
A copy of our current accreditation can be
viewed here.
We also ensure all our suppliers conform to the same requirements and we retain documentation of all relevant EU and US FDA compliance.